Extrusion blow molding bottles are made to hold beverages like juice and pop, liquid soap, detergent, and motor oil for consumer and industrial applications within the food and beverage, automotive, cleaning products, medical, cosmetics, and drinking water industries. Read More…
No matter what your blow molding needs are Western Industries is ready to assist you. We believe in thinking outside the mold and using unique methods to come up with large-part blow molding solutions for our customers. We have access to state-of-the-art technology and over 100 years of combined experience serving a variety of industries. When you choose Western Industries, you have the Western...
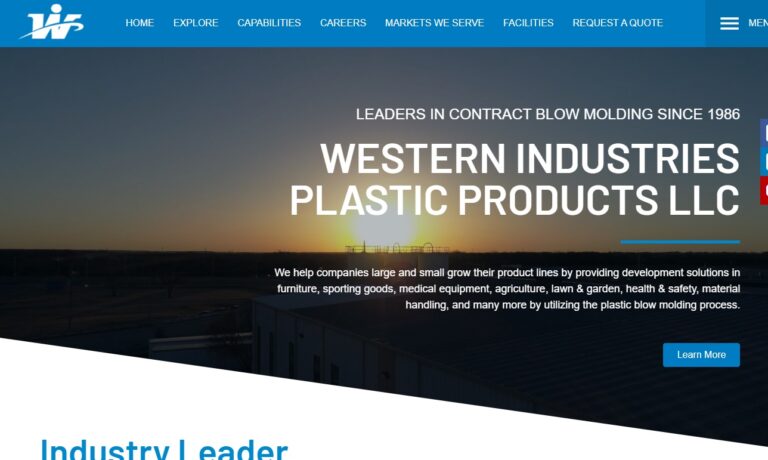
At Lerner Molded Plastics, we specialize in crafting high-quality blow molded products tailored to meet the diverse needs of our clients. With years of expertise in the industry, we take pride in our ability to deliver innovative solutions that exceed expectations.. For more information about our capabilities, contact us today!

With blow molding presses from 1 to 80 lbs., Iceberg Molding has the ability & resources for every step of your blow molding requirements - from a competitive part quote to part & product development support start to finish.
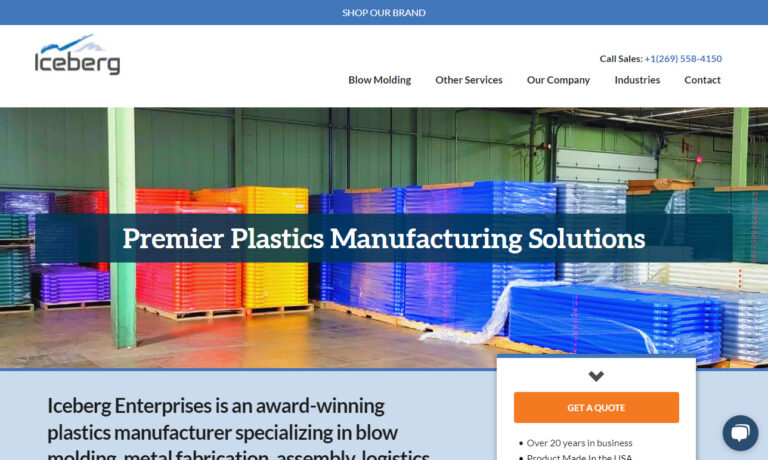
Founded in 1984, Hi-Rel Plastics & Molding, Inc. is a turn-key manufacturer who offers custom blow molding and custom plastic injection molding for a variety of industries. With more than 35 years of experience, our quality products are unparalleled. We process an almost infinite variety of thermoplastic resins, our prices are competitive, our delivery is on time, and we offer superior customer...
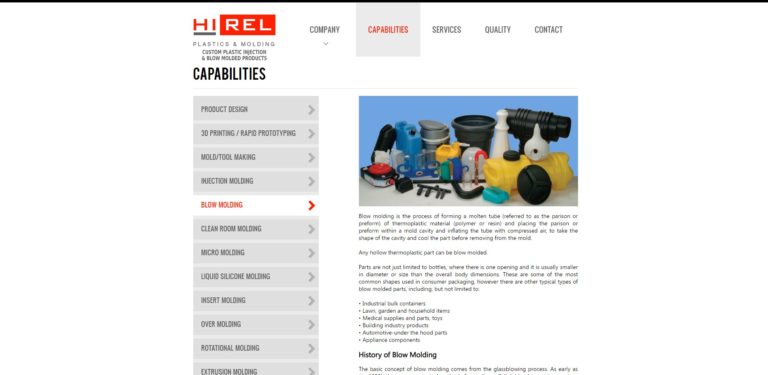
Valencia Plastics is a leading edge blow molder with new methods to add value & ensure superior quality for any job from 10 grams to 3 lbs. Discover our expertise with many plastics & a wide range of machinery. Customers can expect the best from concept to end blow molded plastic product. Industries we serve include aerospace, defense, medical, commercial & pharmaceutical.
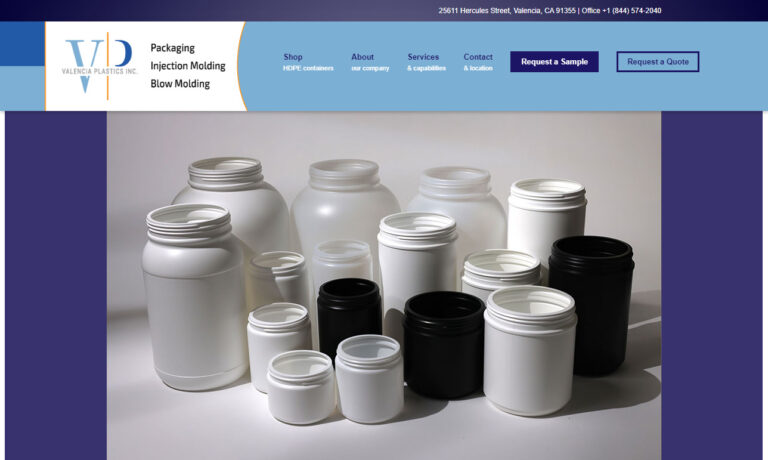
Since 1952, SPI Blow Molding has provided custom blow molding for a diverse range of industries, such as agricultural, plumbing, electronics, and more. Our team can meet your needs with a variety of plastics, such as HDPE, ABS, polycarbonate, and TPE. Secondary operations and assembly services are also available. SPI is a leader in our industry due to our customer-oriented ability to deliver...
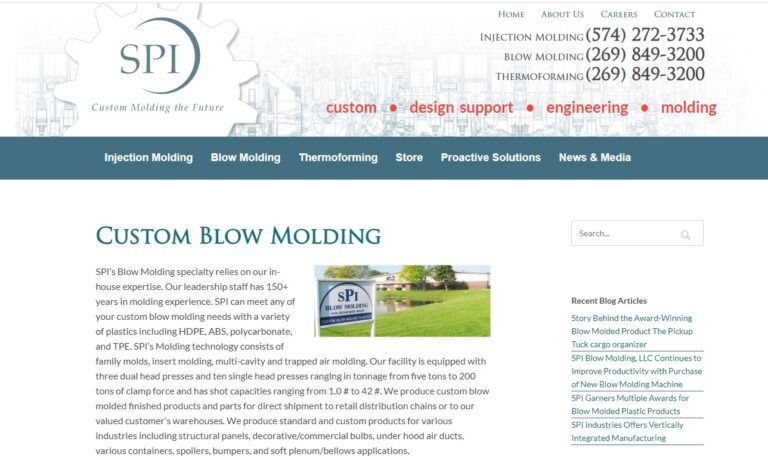
EXI-plast is a full-service provider of custom plastic moulding services, specializing in blow moulded solutions for customers worldwide across a wide variety of industries. With over 30 years of experience developing, producing, and finishing custom plastic products, we have also become a sustainability leader through the integration of postconsumer resins. With products ranging from less than...
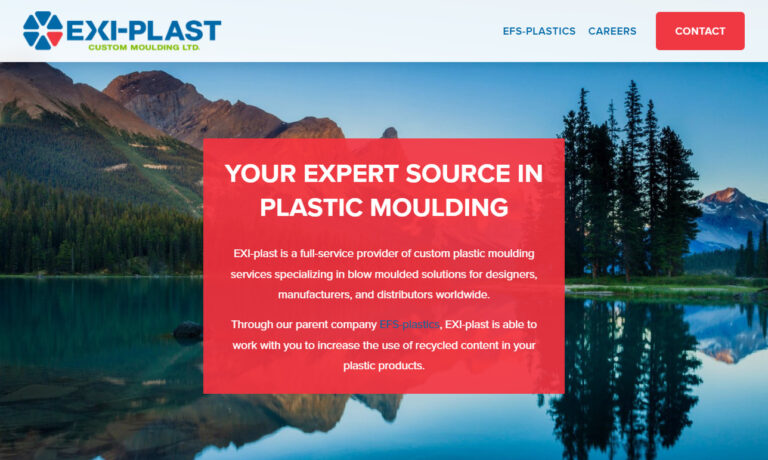
More Extrusion Blow Molding Companies
What is Extrusion Blow Molding?
They are extruded into two mirror molds and have a visible seam dividing the bottle in half. Compared to other blow molding processes, extrusion blow molding generates little waste, all of which is recyclable. In addition, blow molding is distinguished by the hollow tube extruded from the machine to form the pieces.
The name for this tube is a parison. The parison is subsequently encased in a hollow mold, which cycles to the blow station. While another parison is being extruded from the machine, the parison within the mold is molded using air pressure at the blow station, resulting in a shorter cycle time.

Extrusion Blow Molding Process
Extrusion blow molding begins with the formation of a parison, which is a plastic tubular preform. Plastic pellets are loaded into a hopper and fed into an extruder screw with a heating unit. As the pellets pass through the screw, they become molten and are pumped toward the die head.
The liquid plastic flows horizontally and then downward and emerges as a soft tube preform. The preform, called a parison, is then extruded by compressed air as two molds simultaneously come together to form a cavity in the shape of the container. The plastic balloons out and is stretched thin into the mold cavity, taking its shape.
The mold cavity is then chilled by cold water running through the molds. The newly formed part will always have a seam where the two mirror molds came together and a small point at the bottom where the plastic balloon started. Some parts may have excess plastic that needs trimming from the neck or parting lines. The newly formed plastic parts are then put through post forming operations, including drilling, die cutting, milling, painting, and adding decals or labels. Each container or part only takes a few seconds to form and may be done in high volumes. Therefore, they are formed in a continuous or intermittent method.

Machines Used in Extrusion Blow Molding
The two-station and continuous machines are the two types of extrusion blow molding machines. A two-station machine, often known as a "shuttle," moves a common mold back and forth between the extruding parison and the blow station. A continuous, or "wheel," machine continuously produces parts using similar molds.
Larger pieces may be produced using extrusion blow molding than injection blow molding. It's also less expensive, and the part has no internal tensions. However, when utilizing extrusion blow molding, more scrap is created, and there is less control over the correctness of crucial dimensions.

Advantages of Extrusion Blow Molding
- Compared to IBM, EBM offers benefits such as lower tooling costs and the inclusion of blown handle-ware, among others.
- One of the key advantages of IBM is that there is no flash or scrap during processing. It provides the best of all wall thicknesses and plastic distribution control, as well as the ability to mold key bottleneck finishes more precisely. After blowing the plastic melt, the initial IBM preforming cavities are constructed to have the exact dimensions required, accounting for any shrinkage, etc., that may occur. Internal and external neck finishes can be molded with a precision of at least four mil (0.10 mm). It also provides precise weight control in the completed product to within 0.1 g.
Disadvantages of Extrusion Blow Molding
- Controlling parison swell, creating scrap, limited wall thickness control, and plastic distribution could all be disadvantages or restrictions. Blown solid handles can be formed during the BM process if needed. For some designed molds, trimming can be done in the mold, or supplementary trimming processes can be added to the production lines. Scrap is considerably decreased while using 3-D molding.
- Other disadvantages include high tooling costs and the limit to solid handle-ware. In addition, it was previously believed that extrusion blown products were limited to extremely small products (however, large and complex products were fabricated once the market developed).
Choosing the Proper Extrusion Blow Molding Supplier
To make sure you have the most positive outcome when purchasing Extrusion Blow Molding from an Extrusion Blow Molding Supplier, it is important to compare at least 4 or 5 Companies using our list of Extrusion Blow Molding companies. Each Extrusion Blow Molding Supplier has a business profile page that highlights their areas of experience and capabilities and a contact form to directly communicate with the manufacturer for more information or request a quote. Review each Extrusion Blow Molding business website using our patented website previewer to get an idea of what each company specializes in, and then use our simple RFQ form to contact multiple Extrusion Blow Molding companies with the same message.