Blow molding is a method of producing hollow plastic pieces by shaping and connecting them. It can also be used to make glass bottles or other hollow objects. While injection molding and rotational molding are more precise methods of plastic molding, blow molding offers the advantage of high-volume capacity, efficiency, and relatively low costs. Read More…
No matter what your blow molding needs are Western Industries is ready to assist you. We believe in thinking outside the mold and using unique methods to come up with large-part blow molding solutions for our customers. We have access to state-of-the-art technology and over 100 years of combined experience serving a variety of industries. When you choose Western Industries, you have the Western...
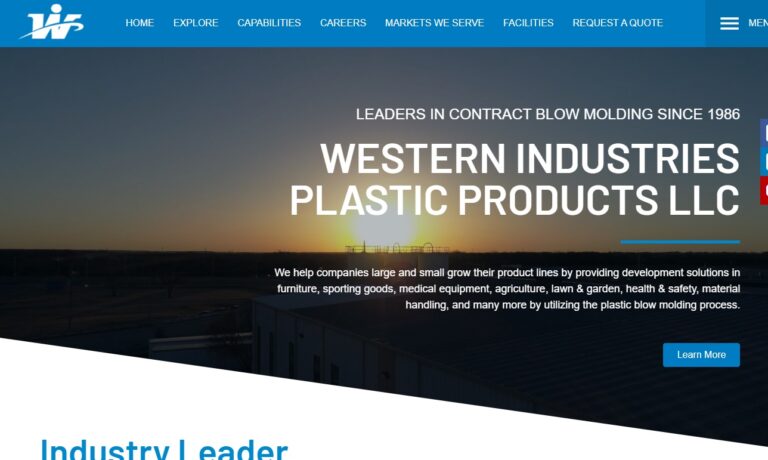
At Lerner Molded Plastics, we specialize in crafting high-quality blow molded products tailored to meet the diverse needs of our clients. With years of expertise in the industry, we take pride in our ability to deliver innovative solutions that exceed expectations.. For more information about our capabilities, contact us today!

With blow molding presses from 1 to 80 lbs., Iceberg Molding has the ability & resources for every step of your blow molding requirements - from a competitive part quote to part & product development support start to finish.
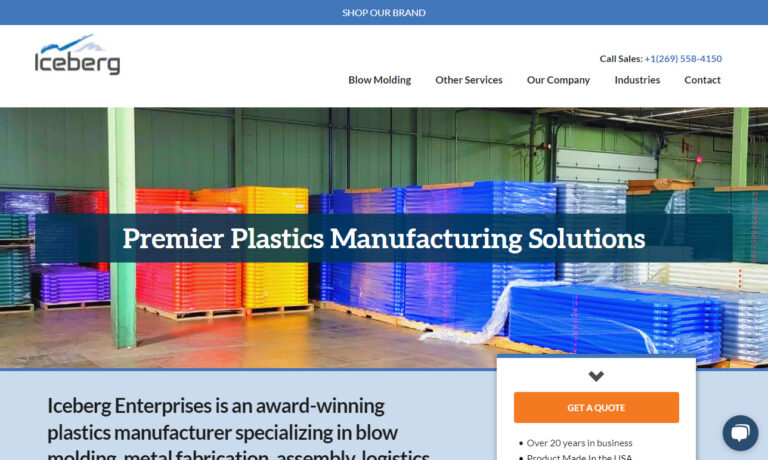
Founded in 1984, Hi-Rel Plastics & Molding, Inc. is a turn-key manufacturer who offers custom blow molding and custom plastic injection molding for a variety of industries. With more than 35 years of experience, our quality products are unparalleled. We process an almost infinite variety of thermoplastic resins, our prices are competitive, our delivery is on time, and we offer superior customer...
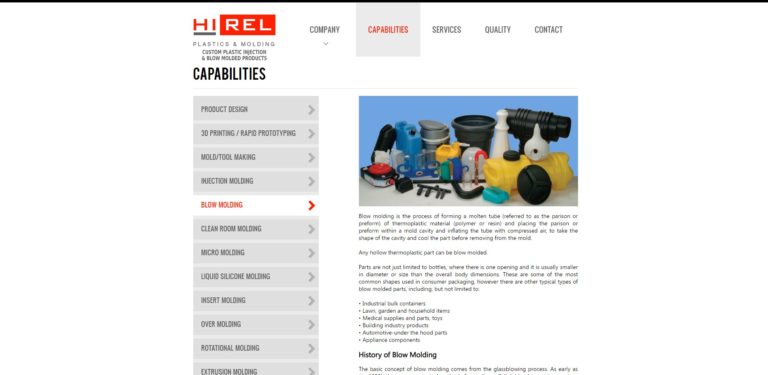
Valencia Plastics is a leading edge blow molder with new methods to add value & ensure superior quality for any job from 10 grams to 3 lbs. Discover our expertise with many plastics & a wide range of machinery. Customers can expect the best from concept to end blow molded plastic product. Industries we serve include aerospace, defense, medical, commercial & pharmaceutical.
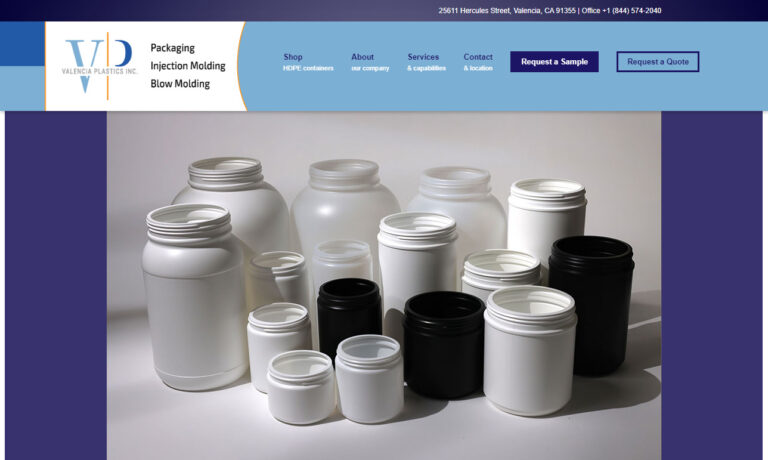
Since 1952, SPI Group has provided custom blow molding for a diverse range of industries, such as agricultural, plumbing, electronics, and more. Our team can meet your needs with a variety of plastics, such as HDPE, ABS, polycarbonate, and TPE. Secondary operations and assembly services are also available. SPI is a leader in our industry due to our customer-oriented ability to deliver successful...
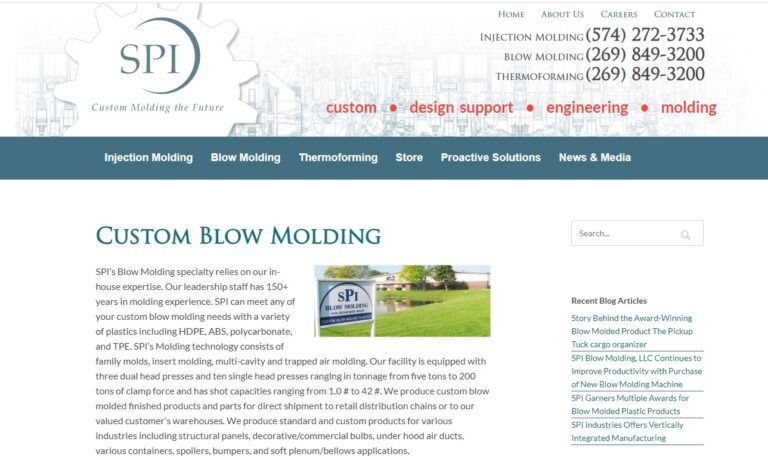
EXI-plast is a full-service provider of custom plastic moulding services, specializing in blow moulded solutions for customers worldwide across a wide variety of industries. With over 30 years of experience developing, producing, and finishing custom plastic products, we have also become a sustainability leader through the integration of postconsumer resins. With products ranging from less than...
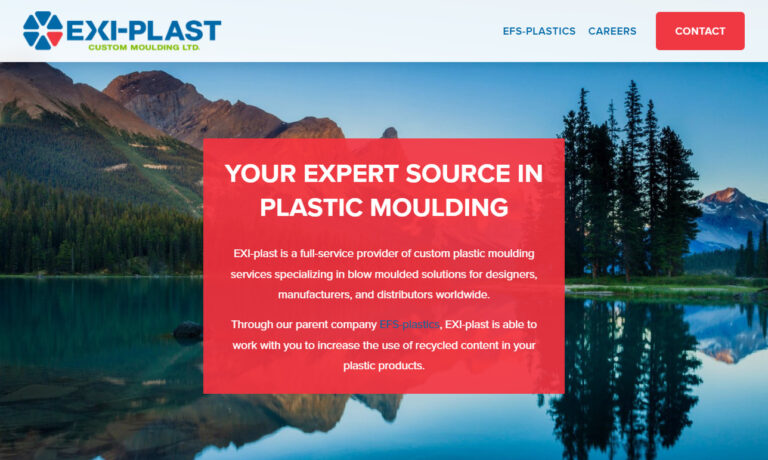
More Blow Moulding Companies
What is Blow Molding?
Blow molding is a method of producing hollow plastic pieces by shaping and connecting them. It can also be used to make glass bottles or other hollow objects. While injection molding and rotational molding are more precise methods of plastic molding, blow molding offers the advantage of high-volume capacity, efficiency, and relatively low costs.
Blow molded products can be formed from standard and common die-cast cavities, but custom blow molding can be used to create specific products for unusual and unique purposes. It is the most well-suited method for forming hollow plastic parts. Thousands of applications benefit from the versatility of the process combined with the strength and durability of the products.

Blow Molding Process
The plastic is melted down and formed into a parison clamped into a mold. A blow pin is then used to force compressed air into the parison, and the molten plastic expands to fit the shape of the cavity.
Controlled and constant airflow is essential to the quality of the final product since varying wall thicknesses compromise the strength and durability of the product. Blow molders have to ensure the constant expansion of the plastic in the mold to achieve uniform wall thickness in the product.
The cavity is cooled, usually by conduction, and the hardened plastic product is removed from the mold, sometimes with the assistance of ejector pins. The process usually takes seconds; blow molding machines can produce high volumes of durable plastic products in short periods with minimal finishing requirements.

Types of Blow Molding Techniques
Injection blow molding, extrusion blow molding, and stretch blow molding are the three most common types of blow molding, which differ during the preform stages. Each variation has specific advantages and application uses, yet the basic process of blow molding is straightforward.
Injection Blow Molding
Injection blow molding is a process in which a plastic preform is injection molded and then transported on a core rod to a blow mold station. Blown air enters through the core rod and lifts the hot preform material off the core rod, forming it to the design of the female blow mold by air pressure.
The blow molds open when the blown plastic bottle has reached the desired shape, and the core rod containing the blown bottle travels to the stripping station, where the blown bottle is stripped off the core rod. After that, the procedure is repeated.
Extrusion Blow Molding
In extrusion blow molding, a plastic material feedstock is supplied through a hopper onto a feeding transfer screw. This feeds material into a specifically designed blow molding die, which guides the flow of material to make a parison, an extruded hollow tube.
Gravity causes this parison to fall until it reaches a process-specific length, causing the mold to wrap around it and seal the bottom edge (giving it the distinctive end seal). A cutting knife splits the parison's open top, and a blow pin advances to the tool's top, inflating the parison against the tool cavity's walls.
The cooled tool walls solidify the molding, which is evacuated after a predetermined time. Finally, the process is repeated with the newly extruded mass of molten glass.

Injection Stretch Blow Molding
Molten polymer flows into the injection cavity via the hot runner block, forming the required shape of the preform with an inner diameter produced by a mandrel (the core pin) and an outer diameter produced by the injection cavity. After a predetermined amount of time, the injection molds and core pins are removed, and the preform supported in a neck carrier is turned 90 degrees.
The preform is ready for stretching and blowing to the finished shape once it has been conditioned to the proper temperature. Once the preform is within the blow mold region, the molds are closed, a stretch rod is supplied to stretch the preform longitudinally, and the preform is blasted circumferentially utilizing two levels of air pressure.
The molds open once a certain amount of cooling time has passed, and the preform is extracted using drop chutes or robotics. In practice, the four phases are completed simultaneously by rotating a carousel of molds.
Choosing the Right Blow Molding Manufacturer
To make sure you have the most positive outcome when purchasing Blow Molding from a Blow Molding Manufacturer, it is important to compare at least 5 or 6 Manufacturers using our list of Blow Molding manufacturers. Each Blow Molding Company has a business profile page that highlights their areas of experience and capabilities and a contact form to directly communicate with the manufacturer for more information or request a quote. Review each Blow Molding business website using our patented website previewer to get an idea of what each business specializes in, and then use our simple RFQ form to contact multiple Blow Molding businesses with the same quote.